Poor ergonomics refers to the design or arrangement of a workspace or equipment that causes discomfort or strain on the body, leading to physical stress and potential injury. There are solutions to ergonomic issues such as changes to workflows that improve worker ergonomics.
Detecting ergonomic issues in industrial settings is the key to mitigating future injuries due to musculoskeletal disorders caused by repetitive stresses on workers. Please request a demo here.
Examples of poor ergonomics include:
- Awkward Postures: Sitting or standing in a position that strains the body, such as hunching over a desk or twisting the neck to look at a computer screen.
- Repetitive Motions: Performing the same motions repeatedly, such as typing or using a mouse for long periods of time, can cause strain on the muscles and joints.
- Excessive Force: Using excessive force to perform tasks, such as lifting heavy objects, can cause strains or sprains in muscles and joints.
- Poor Lighting: Insufficient lighting or glare can cause eye strain, headaches, and neck pain.
- Poorly Designed Workstations: Workstations that are not adjustable to accommodate different body types or tasks can cause discomfort and strain on the body.
- Inadequate Rest Breaks: Working for extended periods of time without breaks can lead to physical and mental fatigue, increasing the risk of injury.
- Environmental Factors: Factors such as temperature, humidity, and noise levels can also impact the ergonomic design of a workspace.
Poor ergonomics can cause a variety of injuries, including musculoskeletal disorders, back pain, carpal tunnel syndrome, and eye strain. By addressing ergonomic issues, employers can improve employee comfort and productivity, reduce absenteeism and injury rates, and improve the overall health and well-being of their workforce.
Poor ergonomics in industrial settings can have a number of negative effects on workers:
- Musculoskeletal disorders: Poor ergonomics can lead to musculoskeletal disorders, such as back pain, neck pain, and carpal tunnel syndrome, which can result in lost time and productivity.
- Increased risk of injuries: Poor ergonomics can increase the risk of injuries, such as slips, trips, and falls, which can result in lost time and productivity.
- Decreased productivity: Workers who are experiencing discomfort or pain due to poor ergonomics may have difficulty concentrating and be less productive.
- Decreased morale: Poor ergonomics can lead to decreased morale and job satisfaction, which can result in high turnover rates and potentially impact the overall culture of the organization.
Overall, poor ergonomics in industrial settings can have negative impacts on worker health, productivity, and morale. It is important for organizations to prioritize ergonomics in order to create a safer and more comfortable work environment for their employees.
Talk with CompScience about our safety analytics solution and workers compensation software.
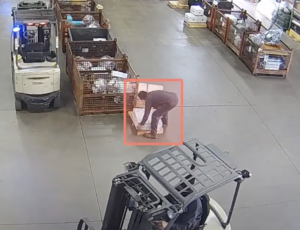